The fusor is a remarkably simple apparatus for producing nuclear interactions between deuterium ions by accelerating them with high voltage electrostatic fields. This post describes the basic theory of operation, construction, and operation of a small low-power fusor that is nevertheless capable of generating a measurable number of neutrons. A notional parts list and references are provided at the end.
Table of Contents
- Operating Principle
- Safety Information
- Vacuum Chamber
- Vacuum Pump
- Deuterium Supply
- Vacuum Gauge
- High Voltage Feedthrough and Cathode
- High Voltage Power Supply
- Neutron Detector
- Operation
- Experimental Results
- Parts List
- References
Operating Principle
From an electrical standpoint, the fusor is a two-terminal glow discharge device with qualitative behavior similar to that of a neon tube. The key difference is that the fusor operates in a regime with lower pressure and smaller separation between the two terminals. Consequently, charged particles (electrons and, more importantly, deuterium ions) are able to achieve very high velocities corresponding to the full acceleration voltage of around 22.5 keV. When two deuterium ions collide at such high velocities, there is a small but measurable probability that the two will interact in the following way, producing a neutron:
{^{2}_{1}H} + {^{2}_{1}H} \rightarrow {^{3}_{2}He} + {^{1}_{0}n} + 3.27MeV
In order to maximize the probability that two positively-charged deuterium ions will collide after being accelerated to maximum velocity, the fusor architecture consists of a small grid-like cathode (negatively-charged electrode) surrounded by a metal vacuum chamber that forms the anode (typically grounded, but positive relative to the cathode). The original fusor invented long ago by Philo Farnsworth had a spherical layout, but the one described in this post has a more linear / tubular form factor. Deuterium ions that are formed on the left and right sides of the chamber are accelerated into the centrally located cathode loops, where they have a good chance of colliding with ions travelling in the opposite direction.

Safety Information
- WARNING: The device described in this post is capable of producing X-rays, ultraviolet light, and a small number of neutrons. The experimenter is responsible for ensuring that no one is exposed to harmful levels of radiation.
- WARNING: High voltage can cause serious injury or death.
- WARNING: Deuterium gas is highly flammable.
- WARNING: All information in this post is provided as-is, free of charge, with no warranty, and for informational purposes only. The experimenter is solely responsible for ensuring safe construction and operation of the device, as well as compliance with any regulatory, legal, or safety-related requirements.
More detailed safety information can be found in the references. Of all the risks associated with operating a fusor, X-ray safety is arguably the most challenging to address. One approach to help mitigate this risk is to construct the vacuum chamber entirely from stainless steel. X-rays produced by 22.5kV discharges have very limited ability to pass through stainless steel or lead, but are able to travel much more easily through other materials such as glass. A second mitigation approach is to stay as far away from the device as possible during operation, as radiation intensity varies inversely with distance squared. Again, this entire post is provided for informational purposes only. The experimenter is responsible for taking all necessary safety precautions, whether or not they are identified in this post.
Vacuum Chamber
The fusor is built around a small vacuum chamber that serves both to maintain a low-pressure deuterium atmosphere and as the grounded anode. The vacuum chamber is a standard KF-50 to KF-25 reducing cross. A cooling fan is also visible in the picture below. Some discoloration of the stainless steel vacuum chamber is evident. This was caused by a previous experiment where the temperature reached excessive heights due to absence of the fan and higher-power operation.

The KF-50 ports may both be covered with blanks, or one of them may be covered with a glass view-port. In the latter case, special precautions must be taken to ensure that no one is exposed to X-rays emitted from the glass port. In any case, the main purpose of having the two capped-off KF-50 ports (instead of using a simple KF-25 straight pipe as the vacuum chamber) is to provide the proper chamber geometry that enables a stable glow discharge to form.
The top of the reducing cross accommodates the high voltage feedthrough and electrode assembly. The bottom is connected to a standard KF-25 four-way cross that links up the vacuum chamber with the diffusion pump, the deuterium source, and the vacuum pressure gauge.

Vacuum Pump
The first step in establishing a low-pressure deuterium atmosphere inside the vacuum chamber is to create a vacuum of below 1 micron. This can be achieved using an oil diffusion pump, backed with a two-stage rotary vane pump.
Oil diffusion pumps are often available on the second-hand market. The one pictured below was probably removed from an old scanning electron microscope. It was acquired for around $150 dollars, but substantial effort was required to refurbish the internal parts which were covered in burned oil. Also, a water cooling system was built using standard PC liquid cooling components. Diffusion pump oil had to be purchased separately, and a 200 volt transformer was also needed. The water-cooled baffle above the pump was purchased separately for around $300. Connection of the non-standard output to the KF-25 cross was a bit of a challenge. A custom adapter (aluminum part above the baffle) was designed using software from emachineshop.com and purchased for a few hundred dollars more, and a gate valve (at very top of the picture) was connected to it. Then, an ISO-63 to KF-25 adapter was used to connect the flat surface of the top of the gate valve body to the KF-25 four-way cross from the previous section. The ISO-63 flange was mated to the gate valve body using a 1/16″ nitrile rubber gasket ring that was cut from a flat sheet.

Unfortunately, the gate valve turned out to be less than useful. The intended purpose of the gate valve was to prevent the powerful diffusion pump from sucking out all of the deuterium gas too quickly. Unfortunately, even when fully closed, the gate valve allowed too much deuterium outflow because it had too loose a gap between the butterfly and the valve body. Instead, a fixed flow restrictor was inserted into the KF-25 connection between the ISO-63 adapter and the KF-25 cross. This was just a simple disk of 1″ outside diameter with an approximately 1/8″ hole in the center. The disk was placed inside the KF-25 connection, with the metal centering ring and 1″ tube holding it in place. This simple part was designed using Adobe Illustrator and fabricated by sendcutsend.com. To prevent high-energy electrons from escaping from the chamber, a second round part with four outer vent holes was also created, and the centering ring was sandwiched between these two custom parts (all shown below).
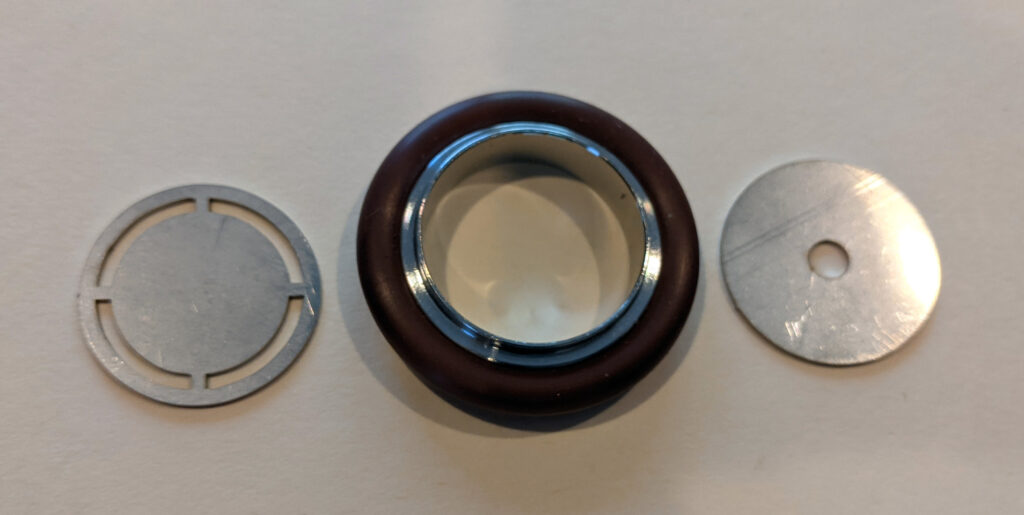
Vapor diffusion pumps require a backing pump. Vacuum equipment suppliers provide high-quality rotary vane pumps for this purpose, but I used a more economical refrigeration service pump, the Robinair 15500 VacuMaster. The pump inlet had to be replaced with a 1/2″ barbed tubing connector, which was then connected to the diffusion pump’s non-standard outlet using a custom-made bracket, flange, and flat nitrile rubber gasket. A second pump is also pictured, but a single pump should be sufficient. The yellow hose from the second pump is connected to a second vacuum gauge that is also not required.

IMPORTANT NOTE #1: The connection between the diffusion pump and the backing pump must be as short and thick as possible. If this connection presents a substantial bottleneck, the pressure at the diffusion pump outlet will build up to such a high level that the pump will either fail to operate or may begin to oscillate. If the vacuum chamber pressure appears to be fluctuating periodically, the most likely causes are (1) insufficient backing pump capacity, (2) inadequate tube thickness, (3) excessive tube length, or (4) excessive deuterium flow.
IMPORTANT NOTE #2: There is one undesirable side-effect of replacing the mechanical pump inlet manifold with a tubing connector. The OEM pump inlet also contains an integrated check valve that prevents the mechanical pump’s oil from getting sucked out if the pump is turned off while it is still connected to a vacuum. If this check valve is removed when the inlet fitting is changed, it is imperative that air be released into the vacuum chamber before shutting down the mechanical pump.
Deuterium Supply
Due to fire safety considerations, the deuterium tank is never connected directly to the apparatus. Instead, a small amount of deuterium is first transferred to a latex party balloon. This balloon is then attached to a tubing connector that feeds a precision needle valve, which is connected to one of the ports on the KF-25 cross. The balloon port is just a piece of left-over 1/2″ hose on a barbed nylon fitting (see parts list for the nylon fitting).

Vacuum Gauge
The most economical gauge for measuring pressures in the 1 micron to 50 micron range of interest is a thermocouple gauge. I used an inexpensive VMV-1 gauge purchased from eBay. It was connected to the KF-25 cross using a couple more adapter parts (see parts list).

High Voltage Feedthrough and Cathode
The most interesting part of the design is the high voltage feedthrough and cathode assembly. It must not only support a high voltage potential, but must also provide a tight vacuum seal. Furthermore, the inner part of the assembly will become white-hot when it is bombarded with high-energy ions, precluding the use of any plastics or other low-temperature materials. Ideally, the assembly should be constructed from refractory metals like tungsten and refractory ceramic insulators such as alumina.

Luckily, it is possible to construct such an assembly without the use of any special metal-ceramic sealing techniques. Instead, a KF-25 to 1/2″ vacuum connector creates an O-ring seal between the alumina tube and the vacuum chamber body. Then, a 1/2″ to 1/8″ adapter with PTFE ferrules is used to seal a 1/8″ pure tungsten rod to the inside of the alumina tube. The adapter does need to be through-bored so that the tungsten rod can pass all the way through, but this can easily be accomplished using a drill and vise or a drill press. Do be careful not to scratch the fitting surfaces that seal against the PTFE ferrules. The most challenging part of the fabrication process is the drilling of a small hole at the end of the tungsten rod, from which to hang the inner grid. I used 1.45mm short length carbide drill bits for this purpose. A small drill press (or better yet, a rotary tool stand) as well as eye protection are definitely required, and drilling several practice holes in a scrap tungsten rod is probably a good idea as well.
The alumina tube is approximately 9″ long, 1/2″ outside diameter, and 1/4″ inside diameter. It is cut from the 12″ tube in the parts list below using a BOSCH DB1043S blade attached to a miter saw, or using a similar but smaller diamond blade attached to an angle grinder. WARNING: Safety goggles and/or face shield are required during cutting.
The actual grid is made from a 1/25″ pure tungsten electrode. Unfortunately, tungsten is too brittle to bend into the required shape at room temperature. However, once it is heated using a blow torch, it can be bent around a metal object such as a bolt to form a 1.15 cm diameter multi-turn coil as shown. Then, the grid is threaded through the hole in the previously described 1/8″ tungsten rod.

Once the entire assembly has been constructed, it is installed in the top-most KF-25 port of the reducing cross. The hole in the coil should be aligned with the long axis of the reducing cross.
High Voltage Power Supply
The high voltage power supply made by the author of this post is available for purchase on eBay:
25kV Negative High Voltage Adjustable Power Supply – AN-25K-50W

The negative high voltage output cable of the power supply is connected to the cathode using the screw terminal butt splice shown in a previous section (see parts list), and the ground lug on the chassis is connected to the vacuum chamber using bare copper wire.
Neutron Detector
I used a Helium 3 neutron detector made by Maximus Energy. The particular model that I purchased appears to have been discontinued, but the NEUTRON-LITE-SI19N is probably a good substitute. Helium 3 detectors are very sensitive to slow neutrons, but the fusor produces fast neutrons. Therefore, the detector is placed inside a 6″ diameter x 12″ long HDPE cylinder with a long bore hole.

Operation
Once the device has been constructed, the first step is to test the vacuum system. The deuterium valve should be closed just until some resistance is encountered. Over-tightening will easily damage this precision valve. Then, the mechanical pump can be turned on. If there are no leaks, a properly functioning two-stage rotary vane pump should be able to bring the pressure down to 50 microns or lower, as measured by the vacuum gauge. Then, the diffusion pump heater, fan, and water pump (if applicable) should be turned on. After approximately 20 minutes, the chamber pressure should drop to below 1 micron. At this point, a latex party balloon containing a small amount of deuterium can be connected to the valve. Care should be taken to avoid contaminating the deuterium with too much air from the atmosphere.
To adjust the pressure, the valve is opened slowly until the gauge shows around 13.9 microns. A very stable reading is required because otherwise, it will not be possible to maintain a glow discharge at the necessary voltage and current levels. If the pressure appears to be oscillating up and down periodically, the pumping system may be unable to support the amount of deuterium flowing through the system. One possible solution is to use a flow restrictor with a smaller hole. This will allow the chamber pressure to reach a higher level without overwhelming the pumps with too much exhaust. On the other hand, if the flow restrictor hole is too small, the pressure may fluctuate too wildly when power is turned on.
When power is turned on, a glow discharge should form between the cathode loop and the grounded body of the vacuum chamber. WARNING: Proper care must be taken to ensure that no one is exposed to X-rays when the high voltage power supply is on. As the voltage is increased above a certain threshold, a small amount of current (around 1 or 2 mA) should begin flowing. If almost no current flows, the pressure is probably too low and the deuterium valve should be opened just a little at a time. On the other hand, if the current starts to increase too rapidly before the voltage reaches 22.5 kV, the pressure may need to be reduced. WARNING: Don’t get too close to the high voltage connector while the power supply is on! Instead, turn it off, make the pressure adjustment, and then turn it back on. After some experimentation, the best operating point for producing neutrons within the constraints of this small power supply was found to be approximately 13.9 microns, 22.5 kV, 2.0 mA.
After the power supply is turned off, the diffusion pump should be allowed to cool down with the fan and water pump (if applicable) still on. Only then should the mechanical rotary vane pump be turned off. CAUTION: To avoid creating a huge mess, make sure to release the vacuum (by opening a valve or removing a cap) right before turning off the rotary vane pump. Otherwise, oil will be sucked out from the rotary vane pump and into the diffusion pump. If this happens, both pumps will require an oil change! If the rotary vane pump inlet has a back-suck prevention valve, this may not apply.
Experimental Results
Helium 3 spectrometers are very sensitive when it comes to detecting small numbers of neutrons, but they also produce spurious background counts. Furthermore, X-rays and electromagnetic interference can also produce counts, making it difficult to confirm that counts actually correspond to neutrons.
Luckily, there is an idiot-proof method to confirm that counts are actually being caused by neutron interactions. If two identical experiments are performed – one with the HDPE moderator and one without the HDPE moderator, and the experiment with the moderator has a significantly higher count than the one without, this confirms that neutrons were actually being detected. Even at a very modest power level of approximately 22.5 kV at 2 mA (45W), a strong level of statistical confidence that neutrons are being produced can be obtained in 10 minutes:
Experiment | Total Counts (10 min) |
Background | 17 |
HV On, No Moderator | 26 |
HV On, With Moderator | 217 |
This quick video (recorded after completion of the more systematic 10 minute experiments listed in the table) shows how the count rate drops when the moderator is removed:
Parts List
The following notional parts list includes most of the components and raw materials that were used to build this system, except for the vacuum pumps and associated parts / accessories. Some of the items were actually obtained from used/surplus suppliers on a one-off basis to reduce cost, but a similar brand new item from an easy-to-work-with supplier is listed here instead even though the cost may be several times higher than that which a determined scrounger would pay. Deuterium gas is also not listed here. Most specialty gas suppliers have the ability to provide it, but are only willing to sell to companies, not individuals.
Some NPT connectors are used in this design. NPT connections are not ideal for vacuum applications. However, they can provide an adequate seal with some caveats: (1) Apply around 1 1/2 turn of PTFE tape to the joint by turning the male pipe in the same direction that will be used to tighten it (so that the tape doesn’t come off during tightening). (2) Avoid purchasing the NPT fittings from non-US suppliers. Some sellers market BSPT fittings as NPT because they look almost identical, but NPT and BSPT fittings will not form a proper seal. (3) Brass-to-brass or brass-to-stainless-steel connections seem to form a better vacuum seal than stainless-to-stainless-steel, possibly because brass is more deformable. This is just an anecdotal observation of mine.
Description | Part # | Supplier | Qty | Total |
Reducer Cross KF-50 to KF-25 | P102658 | Ideal Vacuum | 1 | $230.00 |
KF-25 to 1/2 in Compression | P103773 | Ideal Vacuum | 1 | $89.47 |
KF-50 Blank Flange | P102320 | Ideal Vacuum | 2 | $38.18 |
Hinge Clamp KF-50 Aluminum | P101201 | Ideal Vacuum | 2 | $25.18 |
Centering Ring KF-50 Stainless Steel | P101245 | Ideal Vacuum | 2 | $31.40 |
4-Way Cross KF-25 | P101206 | Ideal Vacuum | 1 | $140.07 |
Hinge Clamp KF-25 Aluminum | P101199 | Ideal Vacuum | 5 | $44.55 |
Centering Ring KF-25 Stainless Steel | P101243 | Ideal Vacuum | 5 | $39.95 |
KF-25 to 1/4 NPT-Female | P101310 | Ideal Vacuum | 2 | $50.48 |
Tungsten Rod, 1/8″ x 12″ | 5137N7 | McMaster | 1 | $66.17 |
Tungsten Electrode, 0.04″ x 7″ | 8000A522 | McMaster | 1 | $3.97 |
Alumina Tube, 1/2″ x 1/4″ x 12″ | 8746K19 | McMaster | 1 | $35.40 |
Yor-Lok Straight Reducer 1/2″ to 1/8″ | 5182K246 | McMaster | 1 | $42.73 |
Yor-Lok PTFE Sleeves, 1/8″ | 5182K974 | McMaster | 1 | $8.03 |
Yor-Lok PTFE Sleeves, 1/2″ | 5182K977 | McMaster | 1 | $6.91 |
Screw-down Butt Splice | 6922K51 | McMaster | 1 | $4.09 |
High-Precision Valve | 7832K21 | McMaster | 1 | $112.67 |
1/8″ NPT-Male to 1/4″ NPT-Male | 5485K31 | McMaster | 1 | $2.44 |
1/8″ NPT-Male to 1/4″ NPT-Female | 50785K26 | McMaster | 1 | $1.70 |
1/4″ NPT-Male to 1/2″ Barbed Nylon | 2974K137 | McMaster | 1 | $8.68 |
Vacuum Gauge | VMV-1 | eBay | 1 | $121.60 |
1/4″ Flare to 1/4″ NPT-Male | 50635K374 | McMaster | 1 | $2.01 |
Helium 3 Neutron Detector | NEUTRON-LITE-SI19N | Maximus Energy | 1 | $995.00 |
HDPE 6″ x 12″ Rod | 8624K58 | McMaster | 1 | $136.97 |
25KV Negative HV Power Supply | AN-25K-50W | eBay | 1 | $798.00 |
TOTAL (not including pumps, D2) | $3035.65 |
References
fusor.net – This forum is the largest single source of information on everything fusor-related. Many experimenters have posted useful information about their work here, and the author of this article would like to thank all the participants of this vibrant community for their valuable contributions. Special thanks to Richard Hull, Andrew Seltzman, Mark Rowley, Liam David, and Steven Haid for their particularly helpful posts.
Electrical Discharges – A good introduction to general theory of sparks, glow discharges, and arcs. This sort of background knowledge is essential for understanding how the fusor works at the level of electrons and ions, and can be very helpful when it comes to diagnosing failures.
Diane’s Fusor Page – This page has lots of info on fusor theory, and also describes some interesting fusor-related experiments.
Building Scientific Apparatus – An excellent textbook on experimental technique in general. The chapter on vacuum technology is especially thorough and relevant to fusor construction. The book also contains info on electronics and particle detection.